13. Чистка и смазка форм
13.1. Чистка форм.
13.2. Смазка форм.
13.3. Виды смазок.
13.4. Способы нанесения смазки.
Срок службы форм зависит не только от надежности их конструкции, но и от ухода за ними в процессе эксплуатации.
Основные требования правильной эксплуатации сводятся к тщательной очистке форм, освобожденных от изделий, к применению хорошей смазки, облегчающей извлечение готовых изделий, а также к рациональной организации текущего и предупредительного планового ремонта форм.
13.1. Чистка форм.
При формовании изделий на металлической форме или поддоне после распалубки остаются мелкие кусочки бетона, поверхности покрываются цементной пленкой, остатками смазки и др. Если форму не чистить, на ней образуется слой затвердевшего бетона, который ухудшает качество изделий и затрудняет их распалубку.
Поэтому формы после каждого цикла формования очищают, применяя для этого различные приспособления.
Машины с абразивными кругами:
- Применяются только для периодической чистки форм (1 раз в 2 – 3 месяца). При этом поверхности формы должны быть гладкими.
При частом использовании таких машин очищаемые поверхности быстро изнашиваются.
Машины с металлическими мягкими щетками:
- Такие машины эффективны только на незапущенных поддонах для очистки их после каждого цикла промывания. Применение жестких щеток не желательно, т.к. царапают поверхность металла, что увеличивает сцепление бетона с поддоном.
Машины с инерционной фрезой:
- Фреза имеет 6 пальцев, на которых свободно висят металлические кольца. При вращении фрезы кольца ударяют по очищаемой поверхности поддона и дробят оставшуюся на нем пленку схватившегося цемента.
Форму очищают по двум схемам:
1) Машина передвигается над формой (форма не подвижна)
2) Форма перемещается под машиной.
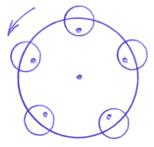
Рис. 70. Инерционная фреза
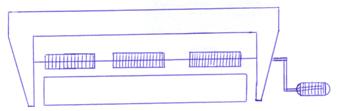
Вид А (сверху)
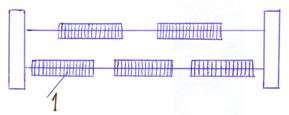
Рис. 71. Блок инерционных фрез: 1 – инерционная фреза
Блок инерционных фрез – 1 – располагаются в шахматном порядке.
После обработки поддона инерционной фрезой все остатки, отделившиеся частицы сметают с поверхности металлическими щетками.
Химический способ очистки форм:
- Основан на свойстве некоторых кислот (соляной), разрушать цементную пленку. Для очистки необходим: 7-15% раствор технической соляной кислоты, в зависимости от толщины пленки, температуры форм.
Например, при увеличении температуры формы с 20оС до 50оС скорость реакции увеличивается в 10 раз.
Химическую очистку форм рекомендуют проводить не более 2-х раз в год.
13.2. Смазка форм.
На качество железобетонных изделий существенно влияет сцепление бетона с поверхностью формы.
Одним из способов уменьшения сцепления является применение различных смазок.
Смазка для форм должна удовлетворять следующим требованиям:
1) По консистенции должна быть пригодной для нанесения распылителем или кистью на холодные или нагретые до 40оС поверхности формы.
2) Ко времени извлечения изделия из формы смазка должна превращаться в прослойку, не вызывающую сцепления с поверхностью форм.
3) Не оказывать вредного воздействия на бетон, не приводить к образованию пятен и подтеков на лицевой поверхности изделия.
4) Не вызывать коррозии рабочей поверхности форм.
5) Не создавать антисанитарных условий в цехах и быть пожаробезопасной.
6) Технология приготовления смазки должна быть простой, позволяющей механизировать процессы ее нанесения.
13.3. Виды смазок.
Смазки, которые применяются на заводах железобетонных изделий можно разделить на три группы.
Таблица 4
Виды смазок
СМАЗКИ | ||
Водные и водно-масляные суспензии | Водно-масляные и водно-мыльно-керосиновые эмульсии | Машинные масла, нефтепродукты и их смеси |
- Водные растворы минеральных веществ (тонкодисперсных) - Известковая - Меловая - Глиняная - Шламовая
Такие смазки просты в приготовлении и имеют низкую стоимость, но не всегда дают хорошие результаты при распалубке изделий. | - Коллоидные системы, состоящие из двух малорастворимых друг в друге жидкостей - прямые; - обратные. Прямые эмульсии («масло в воде»): - Эмульсол ЭКС в количестве 10л на 100л смазки; вода мягкая = 90л, сода кальцинированная = 0,7кг.
Обратные эмульсии ОЭ – 2 («вода в масле») – более водостойкие и вязкие: - 20л ЭКС на 100л - водный раствор (насыщенный извести): - 1г извести на 1л воды = 53л - вода =27л | - Керосин - Петролатум - Машинные масла - Соляровое масло, солидол и зола 1:0,5:1,3 по массе - Соляровое масло, солидол и автол 1:1:1 - Парафино-керосиновая смазка 1:3
Применение таких смазок ограничено их высокой стоимостью.
|
13.4. Способы нанесения смазок.
1) Ручное нанесение.
2) Механизированное нанесение – при помощи удочки или распылителей.