2. Механическая обработка сталей
2.1. Заготовка арматурной стали, поставляемой в мотках (в бухтах).
2.2. Заготовка арматурной стали, поставляемой в прутках.
2.3. Резка сортового и фасонного проката.
2.4. Гибка арматуры.
2.5. Изготовление арматурных сеток и каркасов.
2.6. Виды сварных соединений.
2.7. Изготовление закладных деталей.
2.8. Виды закладных деталей.
Механическая обработка стали для арматурных изделий включает в себя:
- размотку;
- правку;
- отмеривание и резку стали;
- гибку отдельных стержней;
- гибку сеток и каркасов;
- изготовление монтажных петель и другие операции.
2.1. Заготовка арматурной стали, поставляемой в мотках (в бухтах).
В бухтах поставляется арматурная сталь D=3 – 12 мм классов В500, Вр500, A240, A300, A400, Aт400с.
Заготовка производится на правильно-отрезных станках и автоматах.
Одновременно производятся следующие операции:
- правка и чистка.
Отклонения от прямолинейности стержней не должны превышать:
- для D<10 мм – 3 мм на 1 м длины;
- для D³10 мм – 6 мм на 1 м длины.
В настоящее время на заводах ЖБК широко используются правильно-отрезные станки:
- СМЖ – 357 (См. рис. 5);
- И – 6118;
- И – 6022 А;
- ГД – 162.
Принцип работы этих станков одинаков.
Станки имеют:
- подающие ролики, с помощью которых арматура сматывается с бухты;
- вращающийся правильный барабан, где арматурная сталь выпрямляется правильными планками и одновременно очищается;
- отрезное устройство гильотинного типа;
- приемно-выдающее устройство с продольными канавками для направления выправленных стержней и поворотной планкой, закрывающей канавку при приеме стержня и откидывающейся при его сбросе.
- размоточное устройство;
- ограждение.
Установку СМЖ – 357 (рис. 5) выпускают с приемно-выдающим устройством длиной 6 м. Для получения стержней большей длины применяют дополнительные секции этого устройства длиной 2 м. Установка СМЖ – 357 имеет высокую производительность (скорость подачи арматуры 30 – 90 м/мин), позволяет править сталь периодического профиля.
Длина заготовляемых стержней на установке СМЖ –357 от 1000 мм до 9000 мм.

Рис. 5. Установка СМЖ-357 для правки и резки арматурной стали
1 – сборник арматуры; 2 – приемно-сбрасывающее устройство; 3 – электрооборудование; 4 – станок; 5 – ограждение с приспособлением для заправки; 6 – размоточное устройство
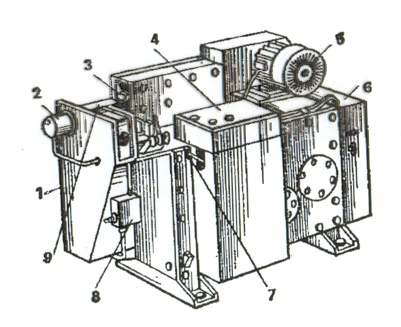
Рис. 6. Станок СМЖ-322А для резки арматурной стали
1 – станина; 2 – гидроцилиндр механизма подпора; 3, 9 – подвижный и неподвижный ножи, 4 – пульт управления; 5 – электродвигатель, 6 – электрошкаф, 7 – переключатель; 8 – напорный гидрораспределитель гидросистемы
Технологическая производительность правильно-отрезных станков зависит от коэффициента использования их по времени, который при хорошей организации труда может быть 0,75 – 0,85.
1) Расчетно-конструктивная производительность станков, работающих по принципу непрерывной подачи арматуры:
2) Производительность станков, у которых на период резки стержней подача арматуры прекращается, зависит от длины отрезаемого стержня:
, (3)
где D – диаметр тянущих роликов, м;
n – частота вращения тянущих роликов, мин-1;
n1 – частота вращения тянущих роликов соответствующая длине отрезаемых прутков, мин-1;
а – масса 1 м круглой арматуры, т;
с – число оборотов ролика за период резки;
К – коэффициент, учитывающий проскальзывание тянущих роликов, равный 0,95 – 0,98.
Для практических расчетов при выборе технологического оборудования используется формула, учитывающая технические характеристики станков:
, (4)
где t - продолжительность смены, ч;
u - скорость подачи и правки, м/мин;
а – масса 1 м арматуры, кг;
Кв – коэффициент использования во времени в течение смены;
a - коэффициент снижения производительности при перерыве подачи арматуры на период резки.
, (5)
где tп – время правки стержня определенной длины, мин;
tР – время резки, мин.
2.2. Заготовка арматурной стали, поставляемой в прутках.
В прутках поставляется горячекатаная арматурная сталь D=10 – 40 мм, классов A240, A300, A400, A600, A800, A1000, A12000.
Заготавливается такая арматура на механических и гидравлических приводных станках для резки арматурной стали.
Заготовляемые стержни должны быть прямыми, без заусенцев и загибов по концам.
Отклонения от прямолинейности на 1 м длины не должны превышать 6 мм.
Серийно выпускаемые станки для резки арматуры по принципу работы разделяются на 2 группы:
- механические: - СМЖ – 172Б;
- СМЖ – 322А (см. рис. 6);
- гидравлические: - СМЖ –133А;
- СМЖ – 175А;
- СМЖ – 214А.
По эксплуатационным качествам наиболее эффективен механический станок СМЖ – 322А.
В одном из исполнений станок комплектуется механизмом противодавления резке, обеспечивающим ровный срез стержня, перпендикулярный к его оси без заусенцев и отгиба конца.
Большая толщина ножей повышает их износостойкость и позволяет работать несколькими гранями с поворотом ножей при износе.
Для особо чистой резки стали, могут устанавливаться ножи с полукруглыми режущими гранями.
2.3. Резка сортового и фасонного проката.
Для резки сортового и фасонного проката, листа и пробивки отверстий при изготовлении закладных сталей следует применять комбинированные пресс-ножницы:
- СМЖ – 229А (см. рис. 7);
- НБ – 633;
- Н – 5222.
Пресс-ножницы СМЖ – 229А предназначены для резки круглого, уголкового, швеллерного и квадратного проката, листа, а также пробивки отверстий и треугольной высечки, необходимых при заготовке элементов закладных деталей.
Пресс-ножницы НБ – 633 и Н – 5222 близки по конструкции и принципу действия пресс-ножницам СМЖ – 229А. Они отличаются в основном повышенной мощностью электродвигателя и некоторыми другими показателями.
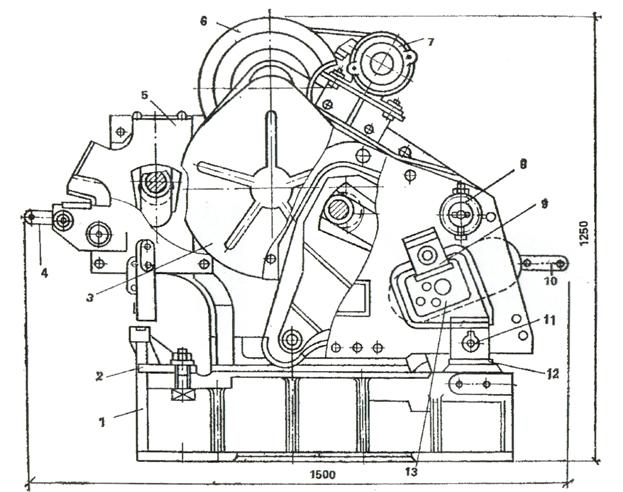
Рис. 7. Комбинированные пресс-ножницы СМЖ-229А
1 – станина; 2 – плита; 3, 6 – механизм передачи; 4, 10 – пусковые рычаги; 5 – ползун; 7 – электродвигатель; 8 – пакетный выключатель, 9, 11 – верхний и нижний упоры, 12, 13 - ножи
2.4. Гибка арматуры.
Для гибки арматурных стержней рекомендуется применять серийно выпускаемые универсальные станки:
- СМЖ –173А (см. рис. 8);
- СМЖ – 179А.
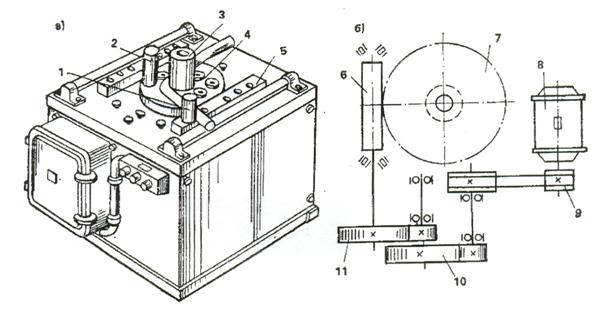
Рис. 8. Приводной станок СМЖ-173А для гибки арматурных стержней
а – общий вид; б – кинематическая схема; 1 – упорный палец; 2 – гибочный палец; 3 – осевой палец; 4 – рабочий диск; 5 – планка с гнездами для установки упорных пальцев; 6, 7 – червячная передача; 8 – электродвигатель; 9 – клиноременная передача; 10, 11 – шестеренчатая передача
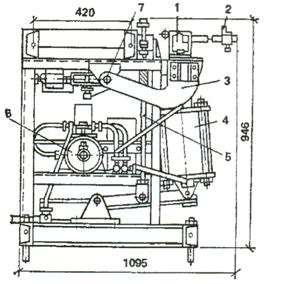
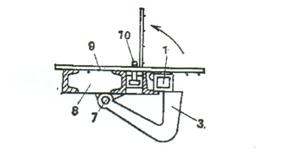
Рис. 9. Станок СМЖ-353А для гибки сварных сеток
1 – гибочная балка; 2 – передвижной упор; 3 – поворотный рычаг; 4 – пневмоцилиндр; 5 – тяга;
6 – коллектор; 7 – шарнир; 8 – стол; 9 – изгибаемая сетка; 10 – пальцы с втулками для прижатия сетки
Принцип работы станков одинаков.
Станок СМЖ – 173А состоит из:
- рамы;
- редуктора;
- плиты;
- приспособлений для гибки прутков;
- электрооборудования;
- педального управления.
В комплект станка входят:
- набор сменных осевых пальцев;
- набор сменных гибочных пальцев;
- набор сменных упорных пальцев;
- набор пластин и оправок, подбираемых в зависимости от диаметра изгибаемой арматуры.
Скорость вращения гибочного диска можно изменять перестановкой шестерен.
Для угловой гибки арматурных сеток и плоских каркасов рекомендуется использовать серийно выпускаемые станки СМЖ – 353А (см. рис. 9) и ПО –725.
Пневматический станок СМЖ –353А предназначен для гнутья сеток и плоских каркасов из арматурной стали диаметром до 12 мм и длиной до:
- 3000 мм;
- 6000 мм;
- 9000 мм.
За несколько ходов гибочной балки станка с перестановкой сетки она может приобрести форму замкнутого контура.
Гибку монтажных петель, хомутов и анкерных стержней следует выполнять на станках СМЖ – 173А и СМЖ – 179А.
Для использования полной мощности станка рекомендуется несколько стержней небольшого диаметра; при пакетном гнутье пользуются специальными держателями.
Производительность станков для гибки стержневой арматуры:
, (6)
где T – фонд рабочего времени станка в смену, ч;
nд – частота вращения рабочего диска, мин-1;
n – число одновременно изгибаемых стержней, шт;
q – масса 1 м арматуры, кг.
2.5. Изготовление арматурных сеток и каркасов.
Арматурные элементы для сборных железобетонных конструкций можно разделить:
- сетки;
- плоские каркасы;
- пространственные каркасы;
- элементы для предварительного напряжения;
- закладные детали.
Сетки – это арматурные элементы из проволоки одинакового диаметра. Чаще всего применяются как монтажная арматура (например: верхняя сетка пустотных и ребристых плит).
Плоские каркасы – выполняют из рабочих и распределительных стержней, используя их как несущие элементы. Плоские каркасы обеспечивают полную систему армирования конструкций в плоскости, перпендикулярной действующим нагрузкам.
Пространственные каркасы – выполняют из рабочей, распределительной и монтажной арматуры, обеспечивающей полную систему армирования конструкций.
Пространственные каркасы для армирования колонн, прогонов, балок, труб, опор и других видов конструкций могут быть:
- прямоугольного сечения;
- квадратного сечения;
- таврового сечения;
- круглого сечения.
При выборе способа сварки соединений арматуры исходят из следующих условий:
- применения сварных соединений и технологии сварки, обеспечивающих наиболее высокую эксплуатационную надежность и наиболее полное использование механических свойств арматурной стали;
- максимально возможного сокращения материальных и трудовых затрат на выполнение сварных соединений при помощи автоматизированных и механизированных способов сварки; эффективных и высокоэффективных сварочных материалов; эффективных методов контроля качества сварных соединений.
2.6. Виды сварных соединений (см. приложение 1).
В процессе производства арматурных работ применяют несколько способов контактной электросварки:
- непрерывное оплавление;
- оплавление с подогревом;
- импульсное оплавление;
- новый прогрессивный способ сварки металлов трением, который отличается высокой производительностью, высоким качеством и стабильностью сварного соединения, низкой потребляемой мощностью (15 – 20 Вт/мм2).
При изготовлении сеток и каркасов применяют, главным образом, контактно-стыковую и точечную сварку и только для стержней больших диаметров используется электродуговая сварка.
Контактно-точечной электросваркой соединяют узлы сеток и каркасов, состоящие из 2-х, 3-х пересекающихся под углом 60 – 90о стержней. Высокое качество сварных соединений обеспечивается правильным выбором основных параметров режима сварки:
- силы сварочного тока;
- продолжительности процесса;
- усилия сжатия электродов.
В зависимости от длительности сварки, силы и плотности сварочного тока разделяют:
- мягкий режим сварки;
- жесткий режим сварки.
Мягкий режим сварки – характеризуется сравнительно большим временем пропускания тока (от 0,5 до нескольких секунд), силой тока = (4 – 8)×103А и плотностью тока = (8 –12)×10-5А/м2.
Жесткий режим сварки – более целесообразен в технико-экономическом отношении, отличается весьма короткой продолжительностью сварки – 0,01 – 0,5 с., при силе тока = (8 – 20)×103А и плотностью тока = (12 –30)×10-5А/м2.
Арматуру из малоуглеродистых сталей можно сваривать при жестких и мягких режимах.
Сварку из низколегированных сталей, свариваемость которых несколько хуже, рекомендуется проводить только при мягких режимах.
Сварку холоднотянутой арматуры во избежание отжига и потери наклепа необходимо вести только в жестком режиме.
Качество сварки зависит от усилия сжатия стержней электродами сварочной машины, которое в зависимости от диаметра и вида арматуры принимается равным от 1 до 10 кН.
Плоские каркасы и сетки можно изготавливать на одно-, двух- и многоэлектродных машинах.
В условиях мелкосерийного производства узкие и малогабаритные сетки, плоские каркасы широкой номенклатуры, а также закладные изделия изготавливают с использованием одноточечных машин общего назначения, которые выбирают в зависимости от диаметров свариваемых стержней, учитывая паспортные характеристики сварочных машин.
В условиях серийного производства сеток и каркасов преимущественно применяют специализированные контактные многоточечные машины автоматического и полуавтоматического действия.
При изготовлении пространственных каркасов используют контактные подвесные машины.
Стыковая сварка арматуры осуществляется на контактных машинах общего назначения и на специализированных автоматических машинах, работающих в единой автоматической линии сварки и безотходной заготовки арматуры.
Одноэлектродные сварочные машины:
- применяют для сварки сеток и каркасов с предварительной заготовкой продольных и поперечных элементов, которые раскладываются в процессе сварки вручную.
Производительность таких машин в большей степени зависит от продолжительности выполнения оператором (сварщиком) вспомогательных операций:
- подача и раскладка стержней;
- перемещение изделия в процессе сварки;
- снятие готовых изделий.
Сварка сеток и каркасов массой более 25 кг. на одноэлектродных сварочных машинах нерациональна, так как повышает утомляемость рабочих и снижает их производительность.
Машина МТМК – 3´100-1 (см. рис. 10, а) выполняет сварку каркасов шириной до 775 мм из предварительно заготовленных продольных стержней D = 5 – 25 мм и поперечных стержней D = 4 – 12 мм. Производительность такой машины составляет 180 м/ч.
Принцип работы машины МТМК – 3´100-1:
- продольные стержни раскладываются и заправляются в подающее устройство машины, а поперечные стержни поступают из бункера автоматически.
Перемещение свариваемого изделия на заданный шаг автоматизировано.
Машина может быть использована для одновременной сварки двух каркасов общей шириной до 700 мм.
Автоматизированная линия И-2АК-1: (см. рис. 10, б):
- предназначена для сварки двухстержневых каркасов шириной от 70 до 900 мм.
Подача продольных и поперечных стержней предусмотрена сначала в правильное устройство, а затем под электроды машины. Производительность такой линии – от 24 до 360 м/ч.
Плоские сетки и каркасы шириной от 600 мм до 3800 мм изготавливают на комплексно-механизированных и автоматизированных высокопроизводительных линиях (см. рис. 11).
В состав линий входят:
- групповые бухтодержатели для продольной и поперечной арматуры;
- правильные устройства;
- узел приема и подачи поперечных стержней;
- многоэлектродная сварочная машина;
- устройство для поперечной и продольной резки сетки;
- пневмопакетирующее устройство.
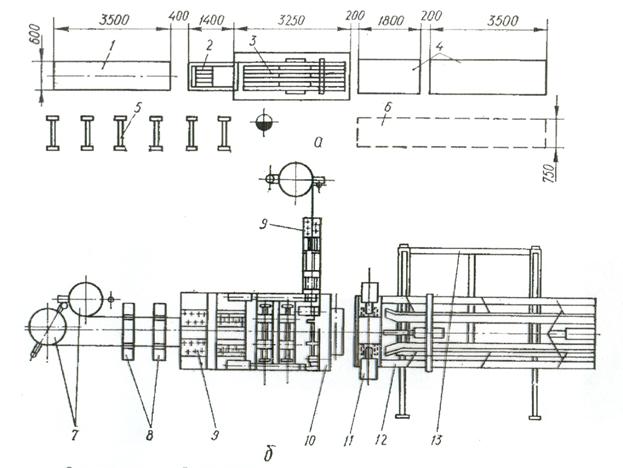
Рис. 10. Схемы организаций технологических линий для сварки плоских каркасов:
а – на машине МТМК-3×100; б – на автоматизированной линии И-2АК-1; 1 – стол для продольных стержней; 2 – каретка; 3 – машина МТМК-3×100; 4 – приемные столы; 5 – стеллаж; 6 – готовые каркасы; 7 – бухтодержатели; 8 – тормозное устройство; 9 – механизм подачи и правки стержней; 10 – сварочная машина; 11 – ножницы для резки каркасов; 12 – приемно-пакетирующее устройство; 13 - контейнер
Основным сварочным оборудованием комплексно-механизированных и автоматизированных линий являются многоэлектродные машины типа:
- МТМС – для сварки каркасов и сеток из предварительно заготовленных продольных и поперечных стержней;
- АТМС – подача продольных и поперечных стержней производится с бухт без предварительной заготовки.
Все операции на линиях, за исключением укладки бухт в бухтодержатели и снятия готовых пакетов или рулонов сеток, автоматизированы.
Применение многоэлектродных сварочных машин снижает трудоемкость процесса и создает возможность рационально использовать производственную площадь.
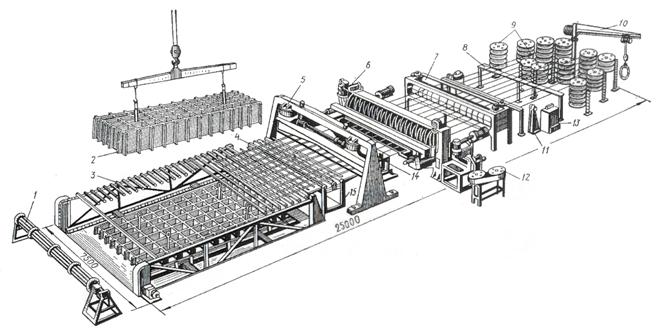
Рис. 11. Автоматизированная линия изготовления широких арматурных сеток:
1 – установка для сматывания сетки в рулон; 2 – контейнер с пакетом сеток; 3 – пакетировщик сеток;
4 – рольганг для перемещения сетки; 5 – ножницы для поперечной резки сетки; 6 – многоэлектродная сварочная машина АТМС-14×75-7; 7 – правильное устройство; 8 – станина с направляющими роликами; 9 – бухтодержатели; 10 – консольный кран; 11 – электроточила; 12 – устройство для поперечной подачи проволоки; 13 – машина для стыковой сварки; 14 – ножницы для продольной резки сетки; 15 – разделитель для укладки сетки
Пространственные каркасы размером в плане 3´7,2 м собирают на вертикальных кондукторах-манипуляторах типа СМЖ – 56А и аналогичных установках спаренного типа СМЖ – 286Б (см. рис. 12). Сварка арматурных элементов производится подвесными сварочными клещами.
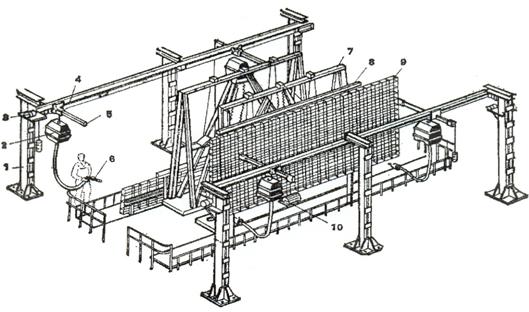
Рис. 12. Вертикальная установка СМЖ-286Б для сборки и сварки арматурных каркасов:
1 – колонна; 2 – трансформатор подвесной сварочной машины; 3 – привод перемещения сварочной машины по монорельсу; 4 – монорельс; 5 – поворотная консоль; 6 – клещи; 7 – рама; 8 – подвижная площадка с кондуктором; 9 – арматурная сетка; 10 – привод механизма подъема площадки
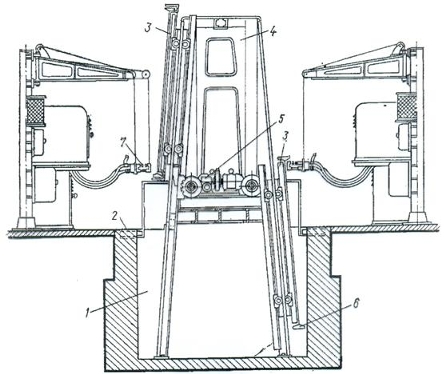
Рис. 13. Установка для сварки объемных каркасов:
1 – приямок; 2 – фундамент; 3 – передвижные рамы; 4 – опорная станина; 5 – привод; 6 – каркас; 7 – сварочные клещи
При массовом производстве однотипных стандартных изделий технологический процесс может быть организован по принципу непрерывного потока с наиболее целесообразной расстановкой оборудования, при которой полностью устраняются возвратные движения.
Большое значение имеет комплексная механизация всех операций технологического процесса, позволяющая снизить трудоемкость производства.
2.7. Изготовление закладных деталей.
Назначение закладных деталей:
Закладные детали, устанавливаемые в изделие при его изготовлении, служат для соединения сборных железобетонных конструкций при монтаже.
В среднем расходуются около 8 кг закладных деталей на 1 м3 сборных конструкций.
Для некоторых типов железобетонных конструкций – до 90 кг (колонны, ригели).
В железобетонных конструкциях следует применять унифицированные закладные детали, которые состоят из элементов профильного проката и анкерных стержней, соединенных между собой сваркой
Изготовление закладных деталей состоит из операций:
- очистка анкерных стержней;
- резка анкерных стержней;
- изгиб анкерных стержней;
- выполнение отверстий в заготовках;
- штамповка рельефа;
- тавровые и нахлесточные соединения.
Заготовленные детали очищают от ржавчины пескоструйными аппаратами.
Для тавровых соединений анкерных стержней из стали класса А240, А300, А400 диаметром 10 – 40 мм с плоскими элементами (Т1-Мф) применяют сварку под флюсом (см. прил. 1).
Применяются полуавтоматические станки АДФ – 2001, производительностью 1000 соединений в смену.
Контролируемые параметры режима сварки:
1) зазор в момент отрыва торца стержня от поверхности плоского элемента;
2) сила сварочного тока;
3) напряжение дуги;
4) продолжительность горения дуги;
5) величина осадки стержня в ванну.
Нахлесточные соединения пластин с анкерами D = 8 – 20 мм (Н2-Кр, Н3-Кп) выполняются контактной рельефной сваркой.
Для этого в элементах листового или профильного проката выштамповывают рельефы, чтобы уменьшить площадь контакта для получения необходимой плотности тока и удельного давления в зоне сварки.
Изготовление закладных деталей электродуговой сваркой допускается в тех случаях, когда нельзя применить сварку под флюсом или контактно-рельефную (так как электродуговая сварка имеет большую трудоемкость).
Последней стадией изготовления закладных деталей является их антикоррозионная обработка.
В заводских условиях чаще всего применяется металлизация – нанесение на поверхность тонкого слоя цинка, алюминия или другого защитного слоя.
Долговечность антикоррозионного покрытия зависит от подготовки поверхности. Поверхность должна быть сухой, чистой и шероховатой.
При нанесении цинкового покрытия проволока Ц–1 D=1 – 2 мм расплавляется и распыляется в металлизаторе струей воздуха под давлением 0,4 – 0,6 МПа. Защитное покрытие наносят по обе стороны пластины.
2.8. Виды закладных деталей.
1) Тавровое и крестовое соединения
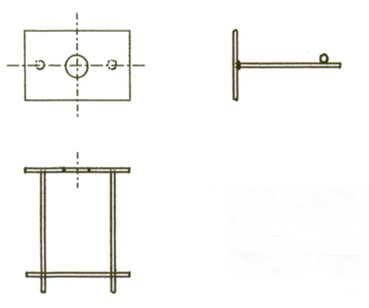
2) Контактно-рельефное соединение
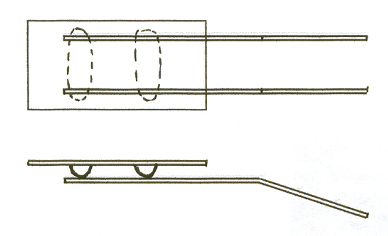
3) Электродуговая сварка
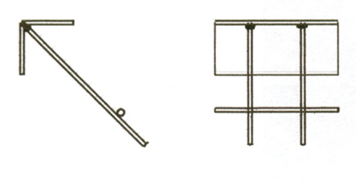
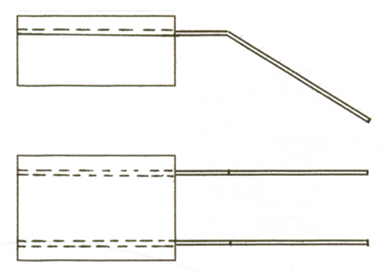